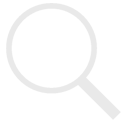
Keeping the air clean provides a safer work environment for all employees. MineTerra understands that controlling NOx, PM, HC, CO and other harmful components makes for a healthier and safer work environment. Our staff has worked in the emissions control industry for 20+ years. We know the products and chemistry needed to reduce harmful pollutants and help keep your work environment safe.
The chemistry of a catalyst coating is critical to meeting required emission reduction targets. It's a matter of knowing the variables that affect conversion of the NO portion of NOx into NO2, and carefully controlling the reactions with advanced catalyst chemistry within the emission control device.
MineTerra has an extensive database of emission control test results generated from equipment being used during real world underground mining. The collected data enables us to determine the best emissions technology for your mining equipment and its duty cycle. Our product line includes advanced solutions that even work on difficult applications such as machines lacking adequate exhaust gas temperature for passive DPF regeneration. At MineTerra, we carefully consider every measurable condition and equipment operating parameter to ensure you have the right product.
We continuously monitor emissions data derived from production machinery and trends in emission regulations to ensure that our customers have the best technologies available for emissions compliance. MineTerra will continue to provide the best combination of low temperature regeneration and low tailpipe emissions, as our customers frequently report. We provide technology that reduces NO2 down to engine out levels and lower.
MineTerra is an industry leading emissions control solutions provider. Our team of experienced professionals have spent their careers working in the field of emission control with the world’s best chemical companies and engine manufactures. Our personnel understand catalyst technology, engines, emissions, regulations and the importance of matching proper catalytic solutions to the demands of each applications requirements. We have successfully implemented solutions for a wide range of applications including: underground mining equipment, stationary gen‐sets, locomotives, and off‐road vehicles. We take pride in ensuring our customers receive the industries best customer service, support and technology. Breathe Easy with a MineTerra emissions control solution on your application.
DISCOVER MORE
MineTerra will closely evaluate your specific application, be it underground mining or diesel locomotive, and tailor a
solution that will utilize the most advanced chemistry available today. At the heart of these solutions, we use
exclusively Corning advanced ceramic cores, on which application specific cutting-edge catalyst coatings are applied. We
leave the metal fabrication portion of the products to skilled close tolerance metal fabrication partners who select the
best stainless-steel materials known to withstand oxidation and impact in the harsh underground mining arena. For those
machines that we have yet to complete a DPF housing design, MineTerra will send a CAD designer for on-site dimensional
take off, with design completion within several weeks.
Where there’s a need to carefully evaluate the duty cycle of a customer’s machine or entire fleet, we connect customers
with independent emission control test specialists. From their careful tailpipe emission sampling and detailed
reporting, we determine which catalyst coating will provide the best combination of low temperature regeneration and low
tailpipe NO2 emissions. In the process of doing so, our products reduce carbon monoxide and un-burned hydrocarbons by
95%+, and particulate matter by 95 – 98%. By installing a simple backpressure monitoring device, the operator stays
informed as to where they are regarding recommended upper limits of backpressure and can therefore schedule DPF cleaning
before exceeding their backpressure limit.
Our approach to each diesel emission reduction opportunity is to first consider use of a passively regenerating DPF. These products do an outstanding job at reducing particulate matter as well as gaseous emissions, so long as they meet duty cycle related temperature criteria. When a machine does not have sufficient exhaust gas temperature to operate with a passive DPF (as pre-determined by operation with a data log device fitted to their vehicle), there are several viable options that will provide outstanding emission reduction performance as well. These systems are considered “active” DPFs, which increase the exhaust gas temperature by several different means. Such systems are costlier and more complex compared to passive systems, but will provide necessary emission reductions, allowing the machine to continue to operate. MineTerra has such systems available and will carefully consider all contributing factors as with passive DPFs and guide the customer to the best available solution.
To ensure logical selection of an emission control system, it’s necessary to carefully monitor the actual machine’s duty
cycle and corresponding temperature profile. Such monitoring is typically done by fitting the subject machine with a
data logging device. Such devices are easy to install and will record the exhaust gas temperature over numerous days
operation. The data is then downloaded and used to generate a profile that indicates a ratio of time / temperature. This
ratio is needed to determine viability of a passive DPF. Testing of gaseous emissions at the tailpipe allows us to make
an educated selection from the numerous DPF coatings in our MineTerra toolbox.
All DPFs need to be accompanied by a back-pressure monitoring device. This is critical to ensure that the engine in a
DPF fitted machine does not experience an episode of excess back pressure due to lack of proper regeneration. Excess
idling, lightly loaded operation, change in diesel fuel chemistry (varying concentration of bio-diesel blends), and
significant decrease in ambient air temperature to mention a few, can cause a DPF to overload with soot, increasing the
back pressure to unacceptable levels.
We provide the industry's best level of on-site service and support, we educate your staff so that they can understand the technology and make the best decisions for your company.
We work tirelessly to ensure that our products are the industry's best combination of Chemistry, Hardware and Software. At MineTerra, we stand behind our technology with our performance warranty.
We take great pride in knowing that our products keep your work site air cleaner and employees safer by reducing toxic emissions.
Electrical Filter Regeneration.
Perfect for low-temperature
applications
Catalyzed wall-flow filters for efficient removal of particulate matter.
Log data and reduce downtime.
Built tough for mining environments.
Our products are built tough with heavy gauge steel to ensure they will last even under the harshest conditions. Our solutions are designed for ease of installation and serviceability. We take pride in the workmanship put into each one of our products.
Passive DPF (diesel particulate filter) technology provides the biggest bang for the buck, so long as the machine exhaust gas temperature is sufficient for proper passive regeneration.
During normal operation, a DPF will accumulate soot (partially burned fuel) until the exhaust gas temperature reaches a sufficiently high temperature at which time the soot oxidizes in the filter. When this occurs, gaseous emissions in the exhaust stream continue to be reduced by 95%+. A catalytic coating applied to the surface of a passive DPF will lower the temperature at which soot will regenerate, reducing overall soot build up in the filter.
Our passive DPFs have been proven many times to provide the best combination of low temperature regeneration while minimizing harmful tailpipe NO2 emissions. NOx (oxides of nitrogen) are generated in the engine's combustion chamber and passed into the exhaust system. When passing through the DPF, part of the total NOx is converted to NO2 (nitrogen dioxide) which helps oxidize the soot in the filter. In knowing what concentration of NO2 in the exhaust stream best oxidizes the soot, we're able to reduce the burden on temperature alone for oxidizing the soot. Most passive DPFs rely on NO2 to assist with regeneration, but other manufacturers are not able to determine the right concentration, either falling short with higher regeneration temperatures, or exceeding a typical industry target of less than 50 ppm NO2 emissions at the tailpipe. MineTerra's DPF coating providers have done exhaustive research to arrive at the best concentration, adjusting each coating to accommodate the different diesel-based fuels used in mining.
The chemistry of the catalyst coating is key. It's a matter of knowing the variables that affect conversion of the NO portion of NOx into NO2 and controlling those variables accordingly. Our advanced catalyst coating partners have proven to be the most effective at controlling these variables, thus providing the best available combination of low temperature regeneration and low NO2 tailpipe emissions across the full spectrum of diesel-based mining fuels.
When there is insufficient temperature for proper passive DPF regeneration, an active DPF system can often be employed. An active DPF will artificially increase the exhaust gas temperature to a level that will oxidize soot that has accumulated in the system. There are several means of increasing the temperature, including an electrically charged heating element upstream of the DPF, boosting exhaust gas temperature, prompting soot regeneration. Some of these systems require that the operator manually start the process on a switch panel, and others start automatically as they sense that back pressure is approaching a pre-set upper limit.
A simple back pressure warning device or magnehelic gauge is sufficient to ensure that pre-established back pressure limits are not exceeded during daily operation.
A data log device provides duty cycle information that is needed to pre-determine if there is sufficiently high exhaust temperature and time at this high temperature, to support the proper functioning of a passive DPF system
It's not necessary to leave a data log device fixed to a machine, unless you would like to continue gathering data once the emission control device is fitted. It's typically beneficial to review temperature and backpressure data once the emission control device is fitted since you will be able to identify trends such as actual exhaust gas temperature as it relates to regeneration of the device.
Fleet managers typically leave a data log device on at least one machine (of each machine model) to evaluate the emission control system performance prior to fitting the same device on other machines of the same model in the fleet.
Portable emission test equipment is usually used to check gaseous emissions downstream from the device. Such testing is typically performed when the machine is stationary, under a "hydraulic stall" (full throttle / full load) test procedure. This emission data is usually compared to the exhaust temperature and gaseous emissions up-stream of the emission control device to determine actual percentage reduction of emission at that point in time. Back pressure at the time of emission testing (still under full load) helps to validate the selection emission control device.
MineTerra can provide retrofit diesel emission control systems for machines fitted with engines that are certified to
EPA Tier 1, 2, or 3 emission levels. Engines that were manufactured prior to these emission standards produce emissions
that are considerably higher in particulate matter, thus will result in rapid plugging and escalating back pressure that
can damage the engines. Machines that have low duty cycle / low exhaust gas temperature can typically be fitted with a
MineTerra actively regenerating filter system that will automatically increase the exhaust gas temperature and
regenerate as needed. These systems, like passively regenerating systems, will reduce particulate matter (black soot) by
95 – 98%, as well as carbon monoxide and unburned hydrocarbons by high 95%+.
Please contact us for a free evaluation of your engine and fuel combination regardless of EPA Tier level and diesel fuel
– biodiesel blend.